FAQ About Thermoforming
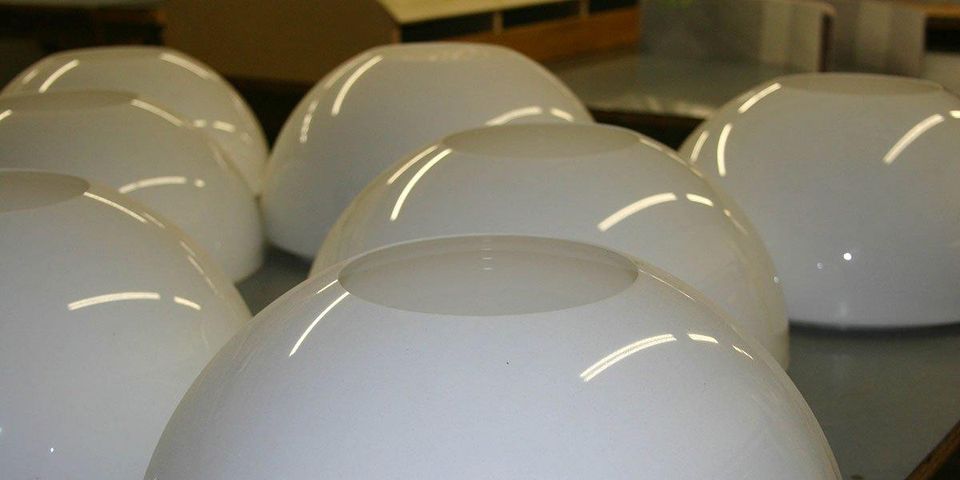
Thermoforming is a fabrication technique used to mold numerous plastic products. To determine whether thermoforming is suitable for your applications, check out these answers to common questions about it.
Questions About Thermoforming Answered
What does the process entail?
To fabricate a plastic product, technicians first put a thermoplastic sheet in an oven. Heat makes the material pliable so it can be placed on a mold. Fabricators use a plug assist, vacuums, and/or pressurized air to seal the thermoplastic to every crevice, corner, and flat surface of the mold.
The material hardens as it cools to create a 3D object. After it’s taken off the mold and trimmed, the thermoplastic form goes through a finishing process where it can be painted, stamped, and labeled.
What types of items are made using thermoforming?
Many common plastic products found in the home are fabricated using thermoforming techniques, including toys, appliance casings, makeup compacts, disposable dishware, and plumbing components. From shipping trays to display boards and auto body parts, thermoforming is also suitable for various commercial and industrial applications.
Which thermoforming method should I choose?
The results you want to achieve should guide the decision on whether to use vacuum or pressure forming for a project. If you need to create a few large products that don’t have too much detail, vacuuming is better suited for your needs. Technicians can complete your small order quickly using this process.
For plastic products with raised patterns, embossed logos, and other intricate features, pressure forming is best.
What plastics can I use?
When deciding what plastic to use, technicians take material thickness and durability into account. ABS plastic is commonly used to create pipes. To form rigid products, technicians use HIPS plastic. HPDE contains petroleum and is lauded for its high-density ratio. It can be used to create both pliable and hard materials.
Since thermoforming is a delicate process, trust the technicians at the Honolulu, HI-based Min Plastics & Supply, Inc. to execute your project and provide high-quality results. From engineering students to contractors, the family-owned company has catered to a range of customers throughout Oahu since 1950. They use a 10-foot-long oven and forming molds to create made-to-order plastic products. To discuss your custom fabrication needs, call (808) 847-1511. Shop the inventory of expanded foam PVC, polycarbonate sheets, Plexiglas®, and additional materials online. You can also check out the team’s work on Facebook.
About the Business
Have a question? Ask the experts!
Send your question