5 Types of Aircraft Corrosion & How to Recognize Them
By AVMATS
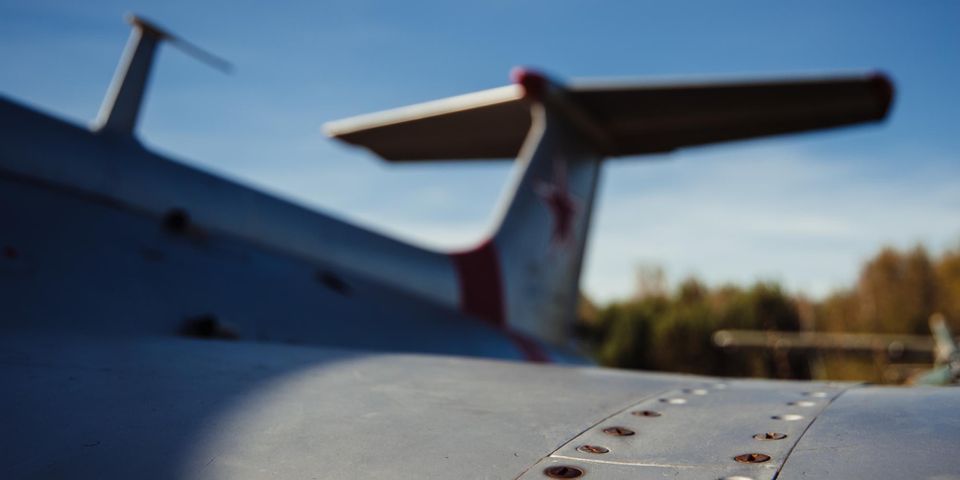
From aluminum to steel and titanium to nickel alloys, constructing an operable aircraft requires many different metals. Due to their toughness, versatility, and lightweight properties, these materials are ideal for aerospace applications. However, they can suffer from corrosion when exposed to extreme weather, moisture, and operational damage. Since corrosion can impact the performance and safety of aircraft parts, it’s important to check for signs of wear during routine inspections.
5 Forms of Corrosion to Look for During Aircraft Inspections
1. Surface
Of all forms of metal deterioration, surface corrosion is the most common and the easiest to spot. Common causes include exposure to chemicals, poor paintwork, air pollutants, as well as humidity. Typically, this damage will make metal surfaces—such as those along the fuselage—appear scratched, pitted, or rough. It is sometimes characterized by flaking paint and a powdery deposit. Filiform corrosion is similar and is identified by worm-like blisters beneath the paint surface.
2. Galvanic
Galvanic corrosion occurs when two different metals—such as steel and aluminum—make contact and experience an electrochemical reaction due to the presence of an electrolytic liquid, such as saltwater. This damage can impact any area where one metal adjoins to a dissimilar metal. It appears as general rusting or discoloration of the metal surface.
3. Stress
When mechanical aircraft parts—such as the landing gear and crankshafts—move, the tensile stress may damage the metal surface. When these scratched areas come in contact with moisture and other caustic elements, stress corrosion may occur. While the damage can sometimes be hard to see with the naked eye, this type of corrosion is known to cause cracks in the metal.
4. Fretting
Although most metals used in aircraft construction are coated for protection, they can wear away—especially if one metal surface continuously rubs against another. Vibration during transit, for instance, can erode two dissimilar metal surfaces that are in contact, allowing fretting corrosion to occur. Fretting corrosion may cause indentations to form on either metal surface. It often occurs near joints or around rivets.
5. Intergranular
Intergranular corrosion is rare but can occur among wing spars, longeron, and other components that use high-strength alloys. This type of corrosion occurs due to temperature inconsistencies during manufacturing and is usually not noticeable until the outer layer of metal begins to flake off.
Providing full-service aircraft inspections and airframe repairs in O’Fallon, MO, AVMATS has the resources necessary to detect all types of corrosion, and if possible, restore compromised metal. If the damage is too extensive, these certified technicians will replace corroded components with high-quality aircraft parts that are manufactured to stand up to extreme conditions. They also offer complete aircraft maintenance services to keep surfaces intact and deterioration at bay. To learn more about their capabilities, visit this aircraft supplier online or call (636) 812-3224.
About the Business
Have a question? Ask the experts!
Send your question