Metal Heat Treating & Removal of Heat Treat Scale
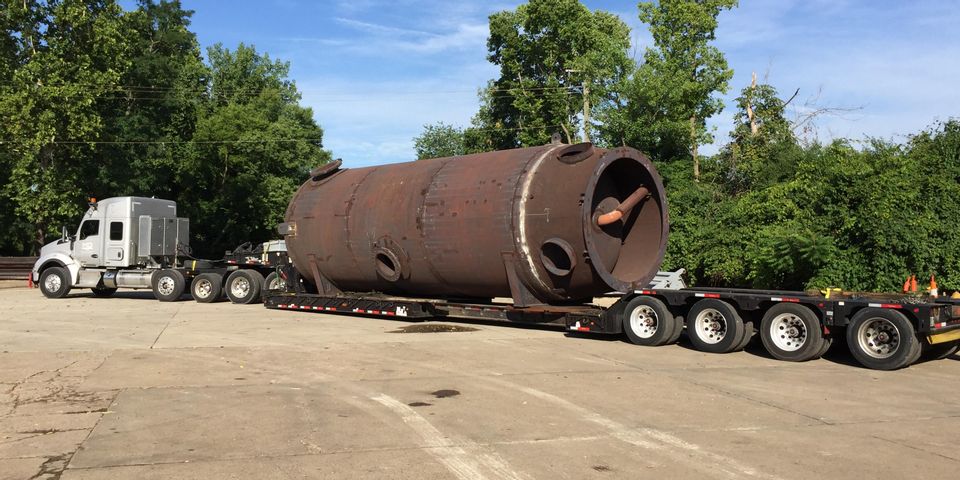
Metal heat treating is a process that intentionally subjects various base metal materials, such as iron, carbon or stainless steels, aluminum, etc., to raised, sometimes extreme temperatures, for specified time periods, with controlled heating and cooling rates to produce desired results.
In addition to base metal materials, various manufactured metal parts such as iron and alloy castings as well as metal equipment and machinery fabrications & weldments are also commonly subjected to some form of heat treatment during production.
The general purpose of the metal heat treating process is to alter the physical (and/or chemical) properties of the material. That is, to affect the very nature of the base metal, or the manufactured parts, to harden, soften and/or strengthen the materials & parts, as part of an intermediary process, or to make them more suitable for their end use.
In some cases, depending on the type of material being heat treated, if the metal heat-treating process is performed in an “uncontrolled atmosphere” at high temperatures, the materials/parts will be exposed to the products of combustion, i.e., Hydrogen and Oxygen. In some materials, this exposure at high temperatures may cause a heat treat “scale” to form on the surface of the material being heat-treated. Heat treat scale is an undesired, dark, usually iron-rich, flaky material on the surface of the material being heat-treated. During subsequent machining this scale can reduce the life of, and/or damage machining tooling, and may cause serious surface defects, on a finished part.
There are a number of methods available to use before, during, and/or after heat treatment, to prevent, and/or reduce the formation of heat-treat scale. One of these methods is a careful & deliberate selection of a base material at the design/engineering phase of the project, which inherently produces little, to no scale during heat treatment. Another method to reduce scaling during heat treatment is to apply a temperature resistant protective coating to the surface of the material prior to heat treatment. Chemical cleaning and abrasive blasting of the material surface after heat treatment are additional options available to remove heat-treat scale.
Abrasive blasting, which typically uses steel shot and/or iron grit or glass bead to remove scale, which is a chemical free process, is the most common method used for scale removal.
The formation of scale on the surface of the material can also be prevented by heat-treating parts in a “controlled atmosphere”, such as argon, or by heat-treating the parts in a vacuum furnace, where the material is not exposed to the products of combustion. (absence of Hydrogen & Oxygen).
Large castings immediately after heat treatment
with dark, flaky heat treat scale on surface
Derrick Company is a metal heat treating company located in Cincinnati, Ohio, offering specialized metal heat treating, blasting and painting services. With more than 80 years in business, this family-owned company has many years of experience processing a variety of parts. Additional services such as abrasive blasting and industrial painting are also available on very large parts, up to 100 feet long & 100,000 lbs.. To learn more about their services, visit them online at www.derrickcompany.com, or call them at (513) 321-8122.
About the Business
Have a question? Ask the experts!
Send your question